Safety and durability remain top priorities when designing and constructing custom staircases. Structural welding plays a critical role in ensuring staircases withstand daily use, environmental factors, and heavy loads. The right welding techniques create seamless connections, enhance strength, and maintain the aesthetic appeal of metal staircases. At Capitol Iron Works, we specialize in designing and constructing high-quality metal and cable railings.
Below, we’ll explore:
- What structural welding is.
- Why it’s critical for staircase safety.
- The welding techniques used in custom staircase fabrication.
- The factors that affect the durability of welded custom staircases.
- How an optimized welding process ensures quality & safety.
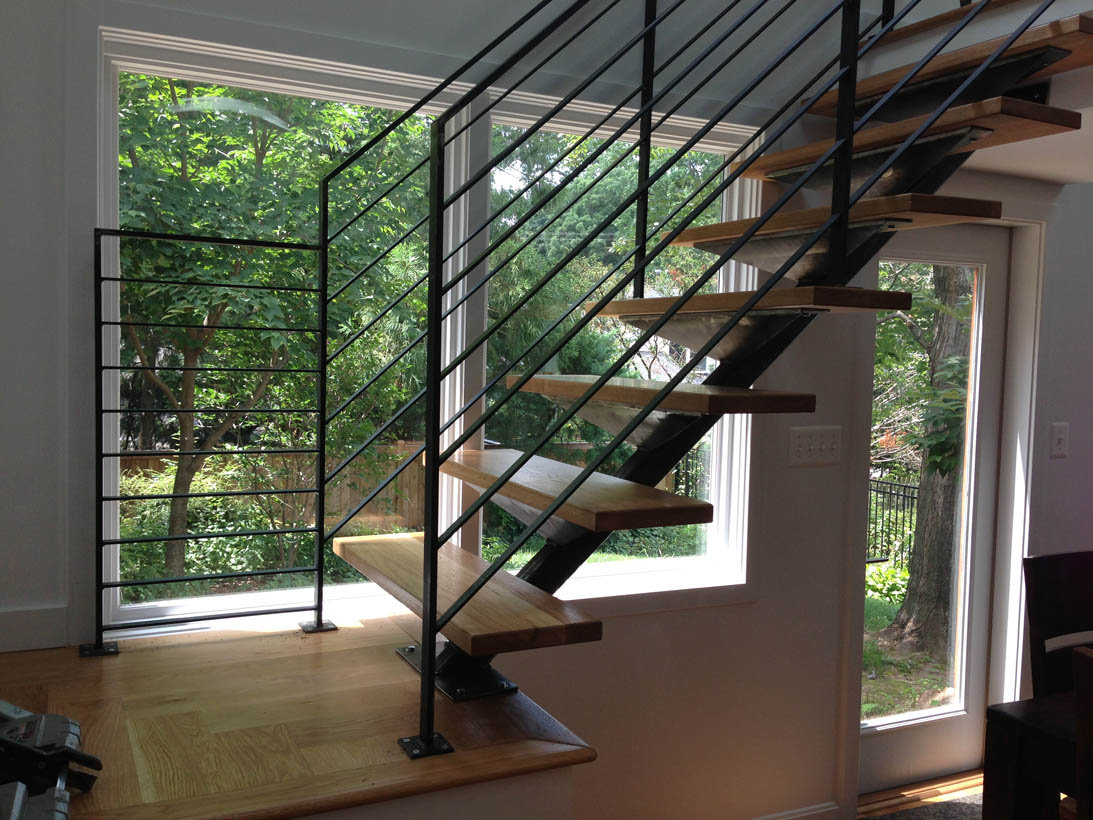
What is Structural Welding?
Structural welding involves joining metal components to create a load-bearing framework. While ornamental welding focuses on decorative elements, structural welding prioritizes strength, precision, and compliance with safety regulations. This technique applies to stair railings, custom railings, and other architectural metalwork. It ensures each staircase meets safety codes while offering lasting durability.
Why is It Critical for Staircase Safety?
- Load-Bearing Strength
- Code Compliance & Regulations
- Seamless Joint Integrity
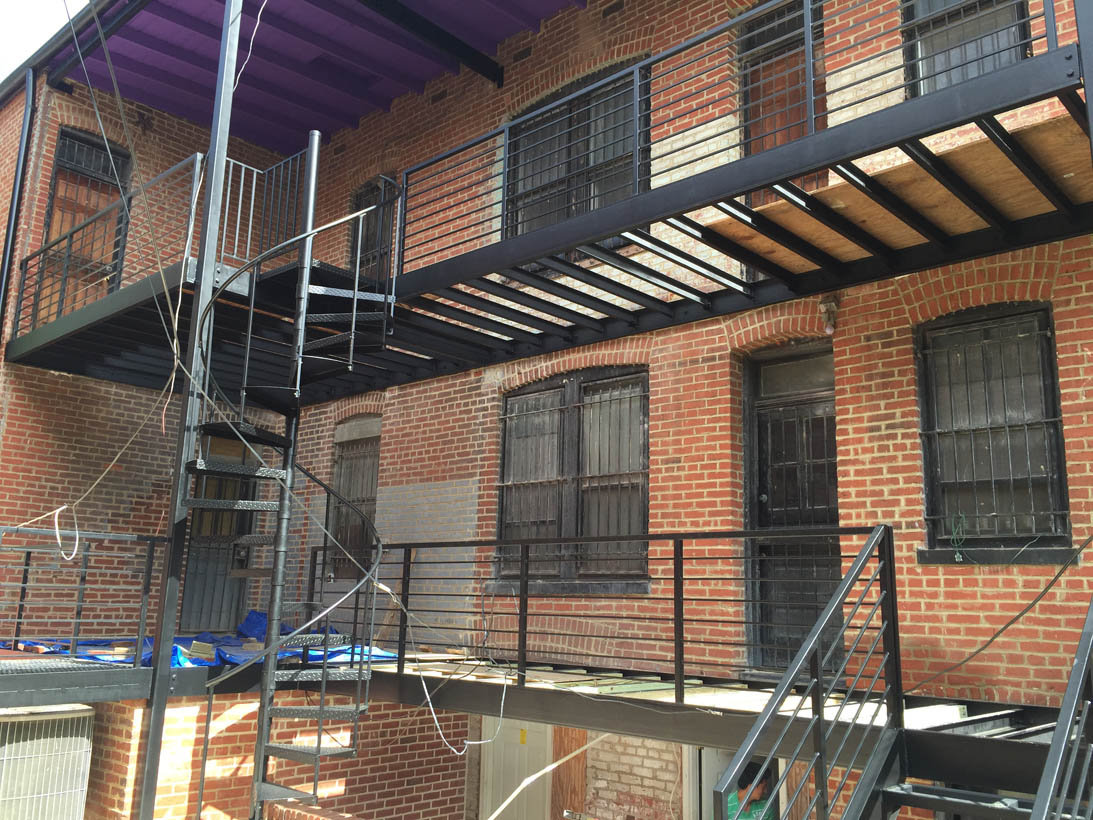
Load-Bearing Strength
Every weld in a staircase must support weight efficiently. Weak welds compromise structural stability, which increases the risk of failure. Professional welding reinforces stair railings and custom railings to ensure they withstand continuous use.
Code Compliance & Regulations
Staircases must adhere to OSHA and International Building Code (IBC) standards. These regulations govern railing height, tread depth, and weight distribution. Proper welding prevents potential safety violations.
Seamless Joint Integrity
Cracked or poorly fused joints weaken over time. High-quality welds provide continuous support by eliminating weak points that could lead to structural failure. This process ensures iron railings maintain their integrity for years. Read “Good Weld vs Bad Weld (and How to Spot Them) | Capitol Iron Works” to learn how to spot quality work.
Key Welding Techniques Used in Custom Staircase Fabrication
- Metal Inert Gas (MIG) Welding
- Tungsten Inert Gas (TIG) Welding
- Shielded Metal Arc Welding (SMAW)
- Flux-Cored Arc Welding (FCAW)
Metal Inert Gas (MIG) Welding
MIG welding provides strong, clean welds ideal for steel staircases and aluminum railings. This process ensures quick application with minimal spatter — a preferred choice for high-traffic areas.
Tungsten Inert Gas (TIG) Welding
TIG welding offers superior precision for smooth, aesthetically pleasing joints. This technique works well for stainless steel, aluminum railings, and glass railings, where appearance matters as much as strength.
Stick Welding (Shielded Metal Arc Welding, SMAW)
Used for heavy-duty structures, stick welding excels in outdoor applications where staircases must withstand extreme weather conditions. Iron railings and metal staircases benefit from its deep penetration and high-strength welds.
Flux-Cored Arc Welding (FCAW)
This method delivers exceptional durability in thick metal components. Custom staircases requiring high load-bearing capacity often rely on FCAW to ensure longevity and structural integrity. Read “ Guide to Different Types of Welding Processes” for more information.
Durability Factors in Welded Custom Staircases
- Material Selection for Longevity
- Protective Coatings & Finishes
- Environmental Considerations
Material Selection for Longevity
- Steel Staircases: High strength and durability with proper protective coatings.
- Aluminum Staircases: Lightweight, corrosion-resistant, ideal for coastal environments.
- Wrought Iron Staircases: Elegant and strong but require rust prevention treatments.
Protective Coatings & Finishes
Powder coating and galvanized finishes enhance corrosion resistance. These treatments extend the lifespan of metal staircases, aluminum railings, and cable railings by reducing their maintenance needs.
Environmental Considerations
Welded staircases exposed to moisture or extreme temperatures require additional protective measures. Sealants and rust-resistant coatings preserve the structure and prevent degradation over time.
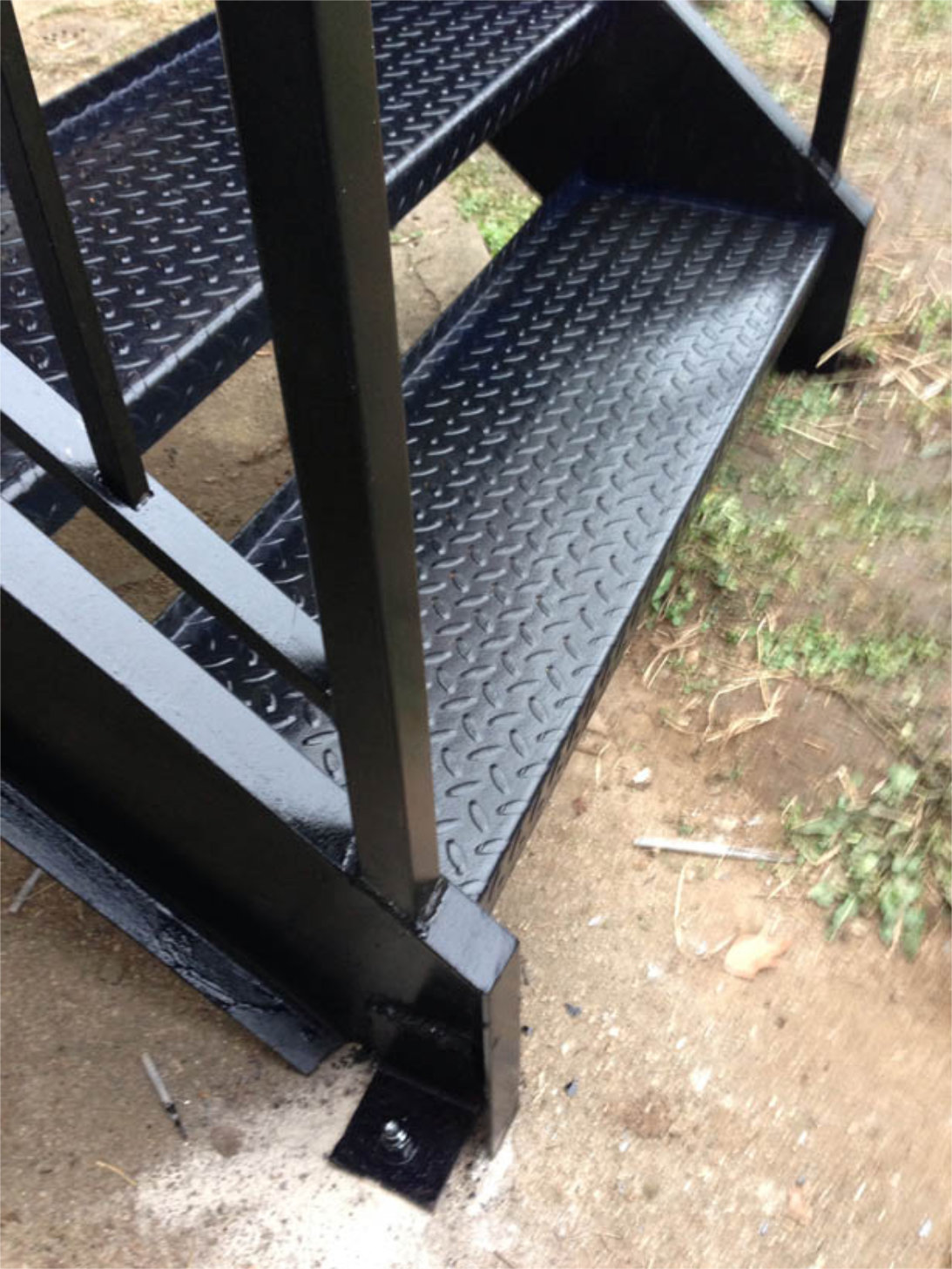
How Our Structural Welding Process Ensures Quality & Safety
- Precision Engineering & Fabrication
- Rigorous Quality Control
- Custom Design Solutions
Precision Engineering & Fabrication
At Capitol Iron Works, we utilize advanced CNC cutting and precision welding techniques to ensure every staircase meets exact specifications. Each weld undergoes thorough inspection to guarantee flawless execution.
Rigorous Quality Control
Non-destructive testing (NDT) verifies weld integrity before installation. Each staircase undergoes multiple inspections to ensure compliance with safety standards.
Custom Design Solutions
Aesthetics and functionality blend seamlessly in our welding process. Our expert fabricators create designs that enhance any space without sacrificing strength. Explore our gallery of past projects to see the quality of our work.
Maximize the Strength & Durability of Your Custom Staircase
Structural welding ensures the safety, strength, and longevity of custom staircases. At Capitol Iron Works, we combine expertise, advanced welding techniques, and high-quality materials to deliver staircases built to last. Our commitment to precision welding, custom railings, and expert railing services sets us apart as a respected leader in our industry. To discuss your custom staircase project and experience the difference professional welding makes, contact us today.