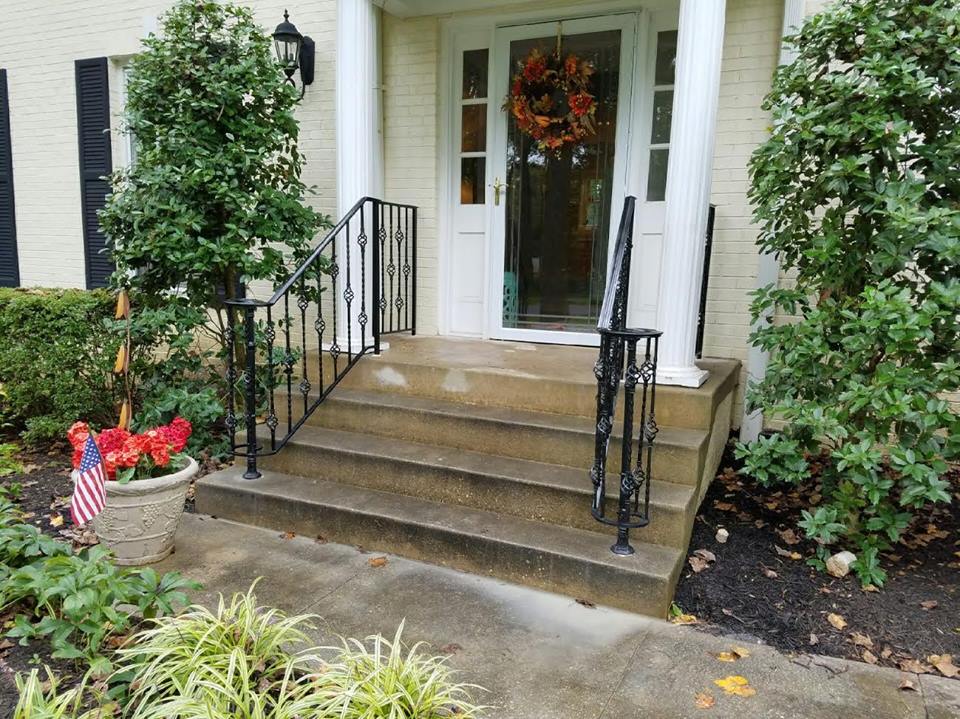
Rust is the silent enemy of exterior iron railings. It weakens structural integrity, diminishes curb appeal, and drives up repair costs.
While most people focus on coatings and paints to stop corrosion, the welding work beneath those finishes plays a far more critical role than many realize.
At Capitol Iron Works, welding isn't just part of the fabrication process — it's your first line of defense against long-term damage.
Why Do Iron Railings Rust Outside?
Exterior iron railings face constant exposure to moisture, air, and airborne pollutants. Over time, this combination triggers oxidation, which turns clean, strong iron into brittle rust.
The risk only increases in humid climates, coastal regions, or during long winters when salt and snow sit on surfaces for weeks. Poorly welded joints, gaps, or areas with uneven welds act like open invitations for water intrusion.
When moisture seeps into these vulnerabilities, rust doesn’t just form on the surface — it spreads from within. Strong welds and intentional craftsmanship are key to keeping this from happening. Without proper fabrication and finishing techniques, even well-designed custom railings can succumb to corrosion over time.
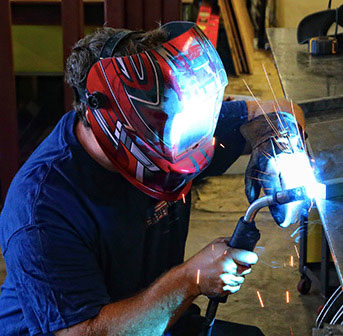
What Role Does Welding Play in Rust Prevention?
Welding creates the structural backbone of any exterior iron railing. But more than that, it determines how well the railing holds up against the elements.
Gaps, inconsistent welds, and exposed seams allow water to penetrate. This accelerates rust and compromises the overall strength of the railing.
By contrast, tight, continuous welds prevent moisture from infiltrating joints. Seamless connections and full weld penetration eliminate weak points, which makes the entire system more resistant to corrosion over time.
4 Best Welding Practices for Rust-Resistant Iron Railings
- Material Preparation
- Choosing the Right Welding Technique
- Full Weld Penetration and Seam Sealing
- Post-Weld Cleaning
Material Preparation
Rust prevention begins before the first spark. All materials must be cleaned thoroughly to remove mill scale, oil, and surface contaminants. Welds made on dirty or oxidized material never bond properly and often flake, crack, or allow moisture beneath the surface.
Choosing the Right Welding Technique
Different welding methods offer different strengths. For most exterior iron railings, MIG welding strikes the right balance between strength, precision, and speed.
Its ability to produce clean, consistent welds with minimal slag makes it ideal for outdoor railings. TIG welding offers excellent precision but is typically reserved for more intricate work.
Meanwhile, stick welding is better suited for heavy-duty industrial applications. Read “Guide to Different Types of Welding Processes” to learn more about the advantages & applications of each welding technique.
Full Weld Penetration and Seam Sealing
Partial welds and tack welds leave open seams where water can collect. At Capitol Iron Works, we prioritize full weld penetration across every joint.
This approach ensures a watertight seal that locks out moisture and strengthens the exterior iron railing from the inside out. Seam sealing also extends to end caps, connections to mounting surfaces, and decorative components.
No part of the railing gets overlooked, and every weld serves a structural and protective purpose.
Post-Weld Cleaning
Once the welding is complete, every joint must be cleaned. This includes removing slag, wire spatter, and any light oxidation that may have formed.
Proper cleaning ensures that coatings or finishes adhere smoothly and effectively. Skipping this step often leads to bubbling, peeling paint, and early-stage corrosion beneath the surface.
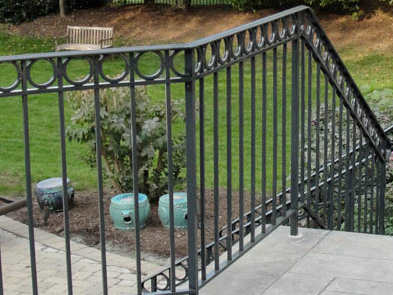
Protective Coatings and Finishing Processes
No matter how strong the welds are, iron still needs protection. At Capitol Iron Works, we apply industrial-grade finishes designed to shield metal from weather, UV rays, and wear.
Powder coating offers an even, durable layer of protection that outperforms traditional paint. Zinc-rich primers and galvanizing methods provide additional protection by bonding directly to the iron surface and forming a barrier against corrosion.
Timing also matters. Applying these coatings shortly after welding reduces the risk of flash rust, ensuring long-lasting durability and aesthetic appeal.
How Our Process Is Different
At Capitol Iron Works, we bring deep knowledge of welding techniques to every custom railing project, whether we’re crafting classic iron railings or sleek custom metal railings.
Each welder on our team adheres to industry best practices, using high-grade materials and meticulous prep work to deliver long-term protection. What sets our railing services apart is the integration of form and function.
We don’t cut corners. Every weld is inspected, cleaned, and finished with care. Whether you're installing exterior iron railings for a historic home or customizing a sleek, modern deck with aluminum or cable railings, our process ensures durability without sacrificing style.
4 Maintenance Tips for Long-Lasting Exterior Iron Railings
Even the best welds need backup from simple upkeep. Routine care combined with strong fabrication methods keeps your investment in top condition for decades.
To extend the life of your metal railings:
- Inspect joints and seams for signs of rust.
- Clean railings regularly to remove salt and grime.
- Schedule touch-ups for scratched or chipped finishes.
- Contact professionals for annual inspections and refinishing when needed.
Ensure Rust-Resistant Exterior Iron Railings with Capitol Iron Works
When it comes to exterior iron railings, rust prevention starts with expert welding. High-quality joints, full penetration, and thoughtful material preparation create a foundation that withstands time and weather.
At Capitol Iron Works, we deliver custom railings built to last by resisting the elements. To learn more about our corrosion-resistant craftsmanship, explore our railing services today.